Some Known Details About Redline Plastics - Rotational Molding - Vacuum Forming
7 Easy Facts About Smak Plastics: Custom Rotational Molding Described
Quickly thereafter, in the '80s, engineers introduced new raw materials, such as nylon and, into the lineup. Utilizing these, they could make plastic fuel tanks,, and industrial molds. In This Author , researchers at the Queen's University Belfast did comprehensive work that led to the advancement of more precise tracking and control systems for cooling processes.
Materials Process To make a rotationally molded item, manufacturers usually utilize a powdered polymer resin, and in truth, more than 80% of the product utilized in rotomolding comes from the polyethylene household. Examples of these plastics include LDPE (low-density polyethylene), LLDPE, PEX and HDPE. Other common rotomolding materials consist of polypropylene,, nylon and polycarbonate.
Polypropylene Polypropylene resin is quite comparable to polyethylene, however it has higher thermal resistance and enhanced mechanical residential or commercial properties. It can also be made clear when uncolored. Polyvinylchloride PVC PVC, or polyvinyl chloride, can be found in both rigid and versatile type. Both plastics have high firmness, great elasticity, excellent chemical resistance, and excellent insulation properties.
See This Report about Iac Injection Molding
Nylon The name "nylon" refers to a whole family of artificial polymers. Generally speaking, nylon products have homes of: high melting point, exceptional abrasion resistance, exceptional colorfastness, durability, and excellent chemical, thermal and UV resistance. Polycarbonate Polycarbonate, which is naturally transparent, is strong, tough, and resistant to heat, with excellent dimensional and color stability.

Plastic Product Manufacturing - Rotational Moulding Company - Excelsior
Stainless Steel Stainless-steel is rust resistant, rust resistant, stain resistant, long lasting and strong. Aluminum Aluminum is a low-density metal with high deterioration resistance. Process Information The manufacture procedure begins with a rotomoulding device with arms called spindles. These spindles support the molds in which the plastic material is included.

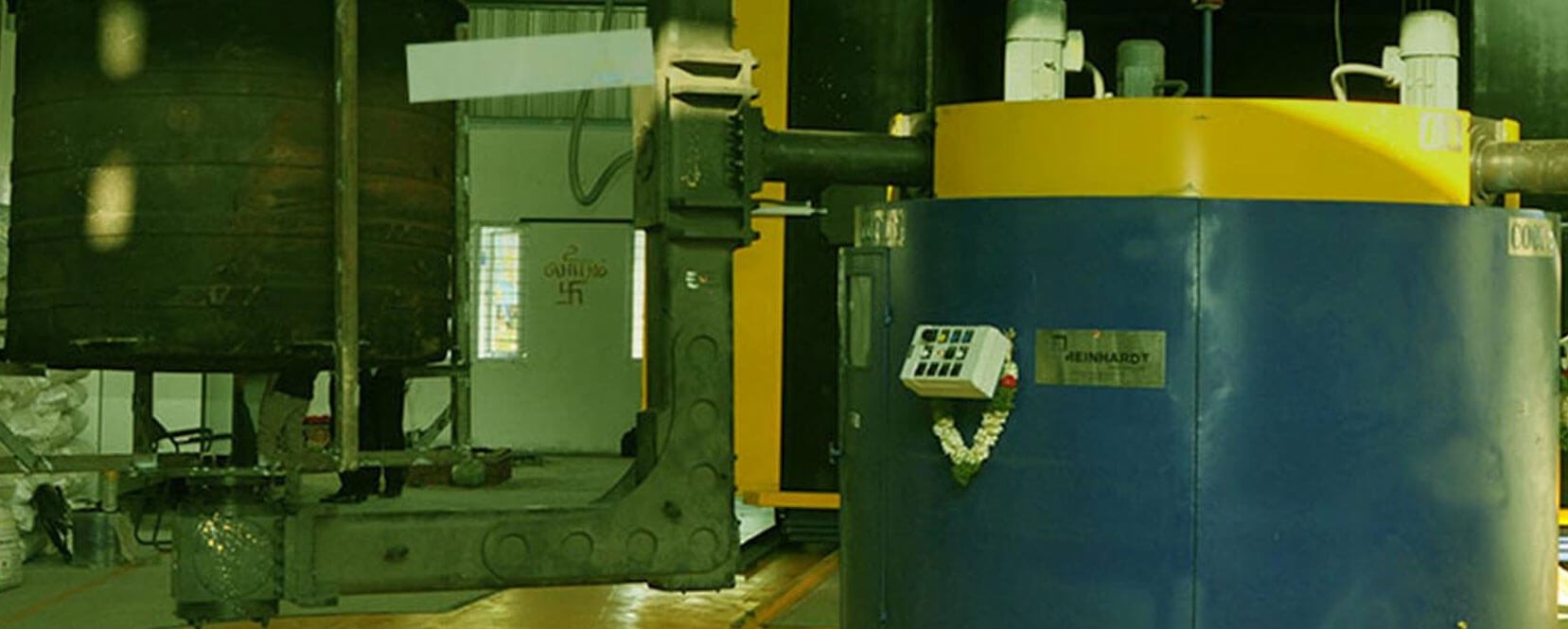
Granger Industries - Granger Plastics Company - Rotomolding - Plastics Rotational Molding
From start to complete, the rotational molding procedure consists four various stages. They are finished in anywhere from 15 to 90 minutes. Stage 1 In the very first stage, which is referred to as the charging phase, the metal mold is packed with a measured amount of raw plastic product and is sealed shut.
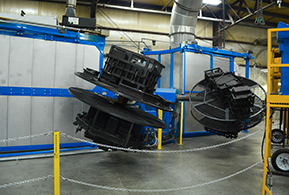
Rotational Molding and Manufacturing - Plastic Resources, Inc.
Little Known Questions About What kinds of products are made with Rotational Molding.
Stage 2 In the 2nd stage, the mold is heated in a heating station, typically an oven, as it gradually turns on the vertical and horizontal axes of the spindles. The axes rotate the mold at varying speeds so that the plastic material does not build up. Rotation continues until the plastic powder is molten and equally covered on the interior walls of the mold.